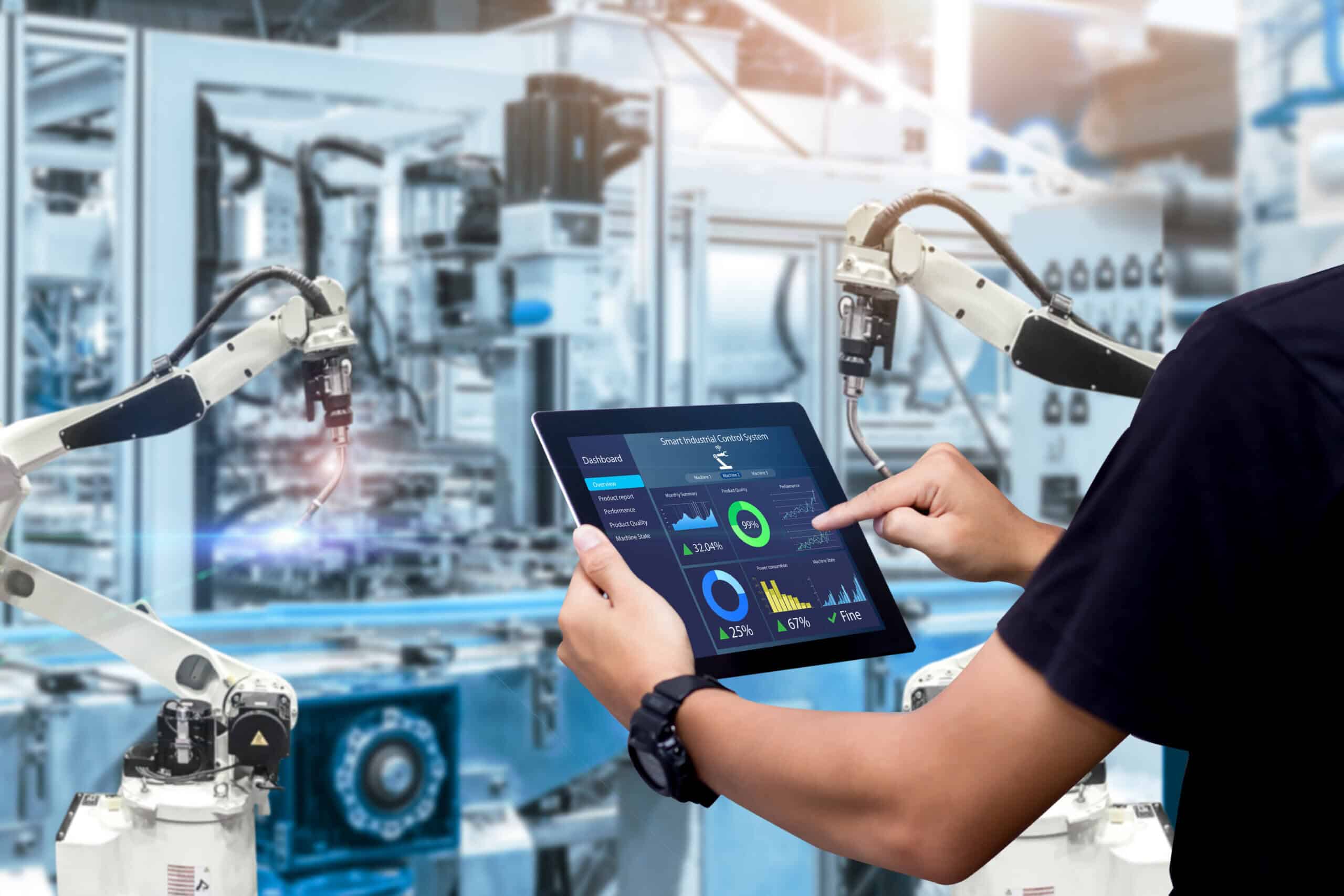
Plastic fabrication has been a critical part of manufacturing for many years, and it continues to evolve with new technologies and trends. In 2023, we can expect to see some exciting advancements in plastic fabrication that will revolutionise the industry. Here are some of the latest plastic fabrication trends to watch out for in 2023:
Plastic 3D Printing
Plastic 3D printing is a revolutionary technology that has completely transformed the way products are designed and manufactured. It allows for the creation of complex shapes and structures with unprecedented precision and accuracy, opening up new possibilities for product development and design.
What is Plastic 3D Printing?
Plastic 3D printing, also known as additive manufacturing, is a process of creating three-dimensional objects by layering melted plastic on top of each other. It is accomplished using a 3D printer, which reads a digital file and then precisely prints each layer of plastic, building up the object layer by layer. The 3D printing process offers many advantages over traditional manufacturing methods, including the ability to produce complex geometries and reduce waste, making it a popular choice for a wide range of industries.
Benefits of Plastic 3D Printing
Plastic 3D printing offers many benefits over traditional manufacturing methods. Firstly, it is much faster than traditional manufacturing, as it eliminates the need for time-consuming and costly tooling. Secondly, it allows for greater design flexibility, as it enables the creation of complex geometries that would be difficult or impossible to produce using traditional methods. Thirdly, 3D printing reduces waste and costs, as it only uses the amount of material needed to produce the final product, minimising scrap, and excess material. Finally, it offers greater control over the manufacturing process, allowing for the creation of custom parts and prototypes that can be easily modified and refined as needed.
Plastic 3D printing is a groundbreaking technology that has the potential to change the face of manufacturing. It offers many benefits over traditional manufacturing methods, including greater design flexibility, reduced waste, and lower costs. While it has some limitations, it has a wide range of applications across many industries, and its future looks bright. As technology continues to advance, we can expect to see even more innovative and exciting applications of plastic 3D printing in the years to come.
Plastic Smart Manufacturing
Plastic pollution is a global environmental problem that has become increasingly severe in recent years. According to the United Nations, the world produces 400 million tons of plastic each year, and much of this plastic ends up in our oceans, harming marine life and contaminating our food chain. To address this issue, manufacturers are looking for ways to reduce their plastic waste and become more environmentally sustainable. One approach that is gaining popularity is called “plastic smart manufacturing.
Smart manufacturing is the integration of advanced technologies such as artificial intelligence (AI), the Internet of Things (IoT), and cloud computing into the manufacturing process. These technologies enable manufacturers to optimise their production processes, reduce waste, and increase efficiency. For instance, smart manufacturing can help plastic fabricators monitor their production lines in real-time, identify issues, and quickly make adjustments to improve their operations. Plastic smart manufacturing is an approach to manufacturing that focuses on reducing waste, increasing efficiency, and improving sustainability. This approach involves using new technologies and processes to minimise the amount of plastic used in manufacturing and to ensure that any plastic waste is reused or recycled.
One example of plastic smart manufacturing is the use of bioplastics. Bioplastics are made from renewable materials such as corn starch, sugarcane, or potato starch, and are biodegradable or compostable. By using bioplastics instead of traditional plastics, manufacturers can reduce their environmental impact and contribute to a more sustainable future.
Plastic smart manufacturing is not only good for the environment, but it can also be good for business. By reducing waste and increasing efficiency, manufacturers can save money on raw materials and energy costs. Additionally, as consumers become more environmentally conscious, companies that embrace plastic smart manufacturing may be able to attract new customers and improve their brand image.
Plastic Customisation
Customisation is becoming increasingly important in the plastic fabrication industry, as more companies seek to produce unique products that stand out in the market. Advancements in technology, such as computer-aided design (CAD) software, have made it easier to create custom parts quickly and cost-effectively. For example, plastic fabricators can now produce personalised phone cases, medical devices, and automotive components using advanced CAD software.
Additive Manufacturing
Additive manufacturing is another trend that’s gaining traction in the plastic fabrication industry. This technology involves building up parts layer by layer using a variety of materials, including plastic. Additive manufacturing offers several advantages over traditional manufacturing methods, including the ability to produce complex geometries, reduce waste, and lower production costs. For example, additive manufacturing can be used to produce lightweight, durable parts for aerospace and automotive applications.
Plastic fabrication is a vital component of the manufacturing industry, and it will continue to witness significant changes in the coming years. With an increased focus on sustainability, technological advancements, and market demands, the industry is set to become more efficient, cost-effective, and environmentally friendly. By staying up-to-date with the latest trends and innovations, plastic fabrication companies can remain competitive and thrive in the ever-evolving market.